Recently our shop has been doing machine work for companies who provide us with the starting material. These companies are using Piping Supplies now because of problems with their current machine shop. We are told these other machine shops have not made delivery times as promised, have not performed the machine work up to their customers’ expectations, and are hard to get answers from. Basically, they are garage and not a professional machine shop.
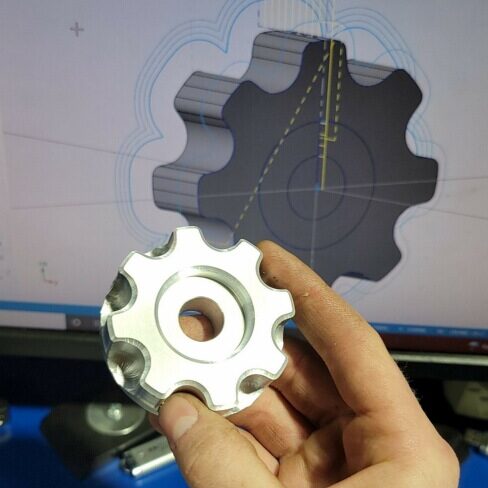
Piping Supplies has been in business in New Jersey for over 50 years. It is easy to forget over time just how professional we are. This isn’t about blowing our own horn as much as it is about recognizing all we do right. There are several things we take for granted:
- The machine shop is open Monday through Friday 7 AM till 4 PM throughout the year. That means material deliveries, order pick-ups, quotes and questions are dealt with quickly. With email, we can be reached during nights and weekends too.
- We ship 98% of our orders correctly and on time. There are a lot of things that go into making this happen. Great material vendors who get us the raw steel we need on time. Employees who show up every day and care about the products they make. Constantly finding ways to improve and machine better and faster.
- We have a quality assurance program which is approved by the highest level in the Navy for supplying nuclear submarine parts. Not only do we have the program, but we actually use it every day. Shortly we will be approved by the International Organization for Standardization, ISO, for their quality management system 9001:2015. Not bad for a small company.
- Piping Supplies has been able to transfer a lot of the knowledge gained in the last 50 years as flange experts to the next generation of owners.
Everyone gets caught up in their own industries and businesses. It is easy to see only the problems we have and mistakes we make. It is nice sometimes to be recognized for how good our work really is and how much we do right. Piping Supplies is lucky to have customers who appreciate what we do and let us know it.