Introduction
Heat exchangers play a vital role in various industries, from power generation to manufacturing and HVAC systems. While the tubes, fins, and overall design of heat exchangers often steal the spotlight, there is a crucial component that quietly ensures their functionality – body flanges. In this blog post, we will delve into the world of body flanges for heat exchangers, exploring their significance, types, materials, and maintenance.
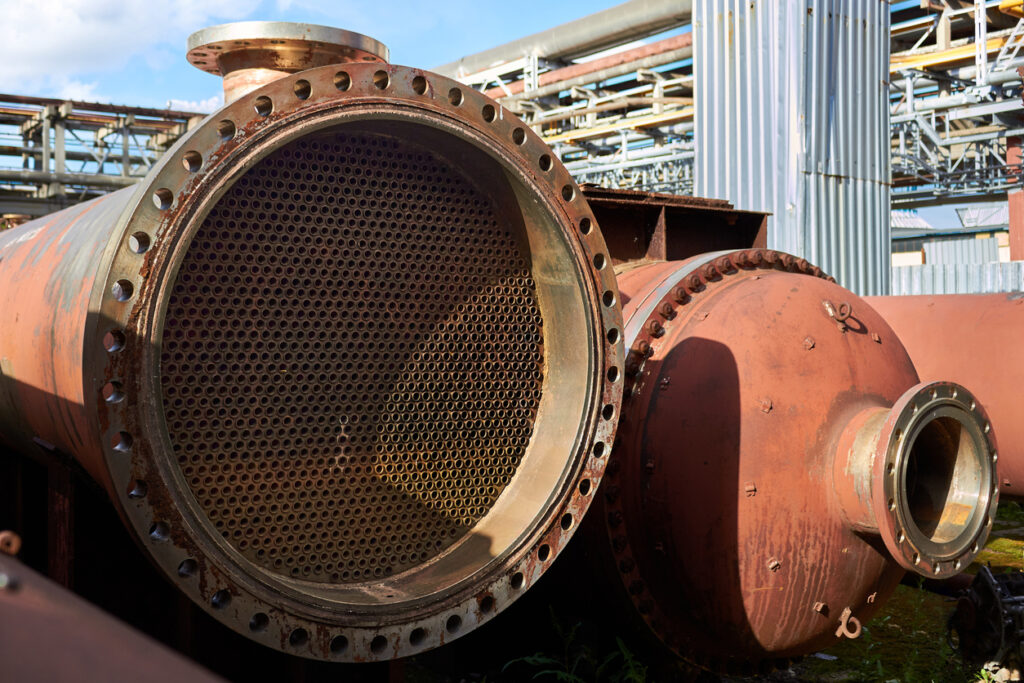
The Role of Body Flanges
Body flanges are the connectors that hold together the various components of a heat exchanger, forming a sealed unit. Their primary purpose is to:
- Maintain Integrity: Body flanges keep the heat exchanger’s structure intact, preventing any leaks or disruptions in the flow of fluids.
- Enable Easy Access: They facilitate the disassembly of the heat exchanger for maintenance, cleaning, and repairs without requiring extensive dismantling.
- Ensure Safety: Properly designed and installed body flanges enhance the safety of the heat exchanger by minimizing the risk of accidents caused by leaks or pressure imbalances.
Types of Body Flanges
- Weld Neck Flanges: These flanges have a long tapered neck that is butt-welded to the heat exchanger shell, providing excellent structural integrity and reducing stress concentration.
- Slip-On Flanges: Slip-on flanges are slipped over the heat exchanger’s pipe end and then welded. They are easy to install and suitable for lower-pressure applications.
- Socket Weld Flanges: Socket weld flanges are connected by inserting the pipe into the socket and then welding the joint. They are ideal for smaller heat exchangers or those operating at moderate pressures.
- Blind Flanges: Blind flanges are used to close off the end of a pipe or heat exchanger tube. They are often used for inspection purposes or to isolate a section of the heat exchanger.
- Lap Joint Flanges: Lap joint flanges consist of two parts – a stub end and a backing flange. They are easy to dismantle and are used when frequent disassembly is required.
Heat Exchanger Materials
The choice of material for body flanges is crucial, as it directly impacts the heat exchanger’s performance, durability, and resistance to corrosion. Common materials include:
- Carbon Steel: Suitable for low to moderate temperatures and pressures, carbon steel flanges offer cost-effective solutions for many applications.
- Stainless Steel: Stainless steel flanges are corrosion-resistant and ideal for heat exchangers operating in corrosive environments or at elevated temperatures.
- Alloy Steel: Alloy steel flanges are used for specialized applications where enhanced strength and resistance to high temperatures are required.
Heat Exchanger Maintenance and Inspection
Proper maintenance of body flanges is essential to ensure the continued performance and safety of a heat exchanger. Regular inspection should include:
- Visual Examination: Inspect for signs of corrosion, cracks, or deformation that could compromise the integrity of the flanges.
- Tightening Bolts: Ensure that bolts or studs connecting the flanges are properly tightened to maintain a leak-free seal.
- Gasket Replacement: If gaskets are used between flange faces, check and replace them as needed to prevent leaks.
- Weld Inspections: If the flanges are welded, examine the welds for cracks, and ensure they meet quality standards.
Conclusion
While body flanges may not be the most glamorous components of a heat exchanger, they are undeniably crucial for its performance and safety. Understanding the different types of flanges, materials of construction, and proper maintenance procedures can help ensure that your heat exchanger operates efficiently and reliably, reducing downtime and maintenance costs in the long run. So, next time you encounter a heat exchanger, remember to appreciate the unsung heroes – the body flanges – that keep it all together.