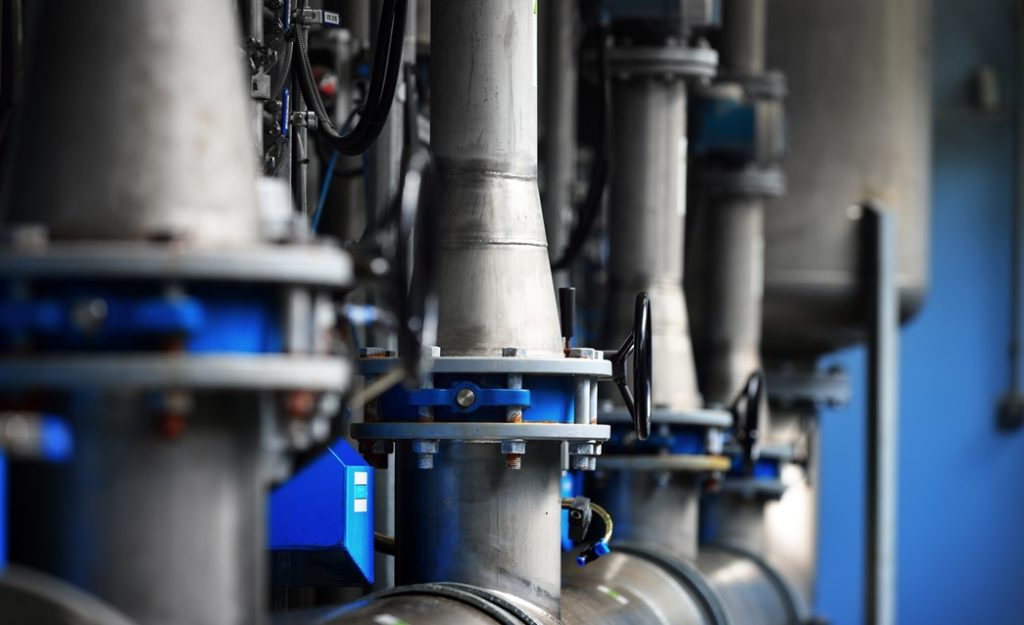
Although it may not be immediately clear from the layman’s perspective, every aspect of industrial construction has been thoroughly thought out. Every joist, truss, beam, pipe, connector and support meets a very specific need. Each component has a job to do and pipe flanges are part of that engineering toolbox. A flange makes it possible to safely and securely connect pipes to each other as well as various surfaces. The bolts and gaskets that complete the package also help ensure integrity of the system. In fact, it would be impossible to design flanges without accounting for the seal that a gasket provides as well as the locking properties of a bolt. Readers who have a need for pipe flanges as part of an upcoming project are encouraged to continue reading and discover the various design types and their best applications.
Pipe flanges can be threaded, socket weld, slip-on, lap joint, weld neck, blind or another form of custom connection. Different applications will call for different designs. A male-female threaded connection is often the simplest to design and work with. A socket weld flange is often called for in low-temperature settings when small pipes are in use. A slip-on, weld neck and lap joint flanges also requires welding but different types to suit the traits of the flange itself. The blind flange, which essentially terminates the flow of liquids and gas through the network of pipes, can show the stopping power of a flange, gasket and bolts when used correctly. Design doesn’t end with the types mentioned above. The face of the flange will also vary and serve different purposes. Flanges can have a flat, raised or ring joint faces. Tongue and groove as well as male and female faces will aid in alignment and gasket seal.
A firm that has proven its capability in creating pipe flanges will ask clients about the dimensions they need for the project. Since pipe diameter is going to vary between applications in a commercial setting, flange diameter, bolt circle diameter, thickness and bore size will also vary between jobs. Those maintaining pressurized systems will also have safety considerations in mind so pipe flanges with the correct size and specifications will help create peace of mind. A larger bolt bore is great if you want to ram home beefy connectors; just be sure that the rest of the flange is up to the task and is large enough to handle the stresses. A machinist who is accustomed to the task of making high-pressure pipe flanges out of steel, alloy, copper-nickel and/or aluminum will be able to help clients narrow down the needs for the job at hand.